The Quiet Killer: Neglected Air Systems
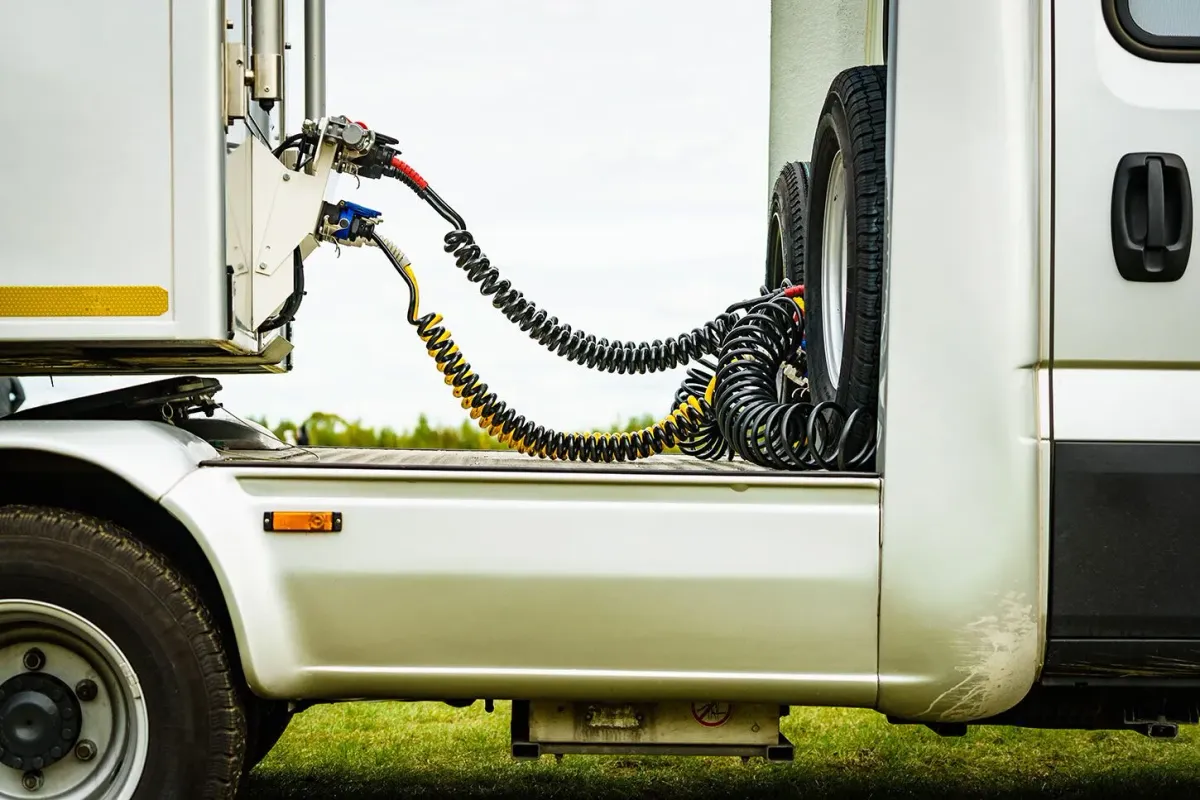
There are few systems on a commercial truck as critical—or as quietly taken for granted—as the air system. It’s the kind of technology that just works, until it doesn’t. And when it doesn’t, the consequences come hard and fast: locked-up brakes, lost loads, jackknifed trailers, and at times, lives changed in an instant.
Yet despite its central role in safe, reliable operation, the air system doesn’t get the same attention as engines, tires, or transmissions. It doesn’t leak oil on the pavement. It doesn’t rattle under the hood. It doesn’t flick on a warning light you can’t ignore. Instead, it degrades in silence, across thousands of miles and countless brake applications—until one day, something sticks, snaps, or freezes, and a driver finds out the hard way.
In this industry, where time is money and margins are thin, there’s a dangerous tendency to focus maintenance efforts on what screams the loudest. The check-engine light. The worn tire. The rattling fan clutch. But air systems? They whisper. And if no one’s listening, they can kill.
Let’s take a moment to understand why neglected air systems are among the most serious—and preventable—threats facing commercial fleets today.
An Invisible Burden
Air systems are often described as the lifeblood of a truck’s braking operation, but that doesn’t quite capture the reality. They're more like the nervous system—constantly regulating, adjusting, pulsing through a network of lines, valves, dryers, and reservoirs. Every time a driver touches the brake pedal, they're depending on that unseen network to respond instantly and precisely. There’s no cable, no hydraulic fluid, just pressurized air—created, stored, and directed by a system that operates in silence.
And therein lies the problem.
When a tire is worn, you see it. When oil burns, you smell it. But when air dryers stop pulling moisture from the lines, or a brake valve begins to stick in cold weather, there’s no obvious sign—not at first. The degradation of an air system is cumulative, invisible, and often goes unnoticed until there’s a failure that can’t be ignored.
It’s this quiet deterioration that makes air systems so dangerous. Drivers assume everything is fine because the brakes still respond. Shops overlook deeper inspections because everything passes a basic function test. Dispatchers don’t log complaints because no one's made one. But behind the scenes, water builds in the tanks. Rust forms in the lines. Plastic air lines chafe against frames. And those tiny imperfections begin to set the stage for something much bigger.
The Fragility of Routine
One of the toughest things to combat in fleet operations is the normalization of risk. If a driver gets used to a slow brake release, or a shop brushes off an intermittent air leak, it becomes part of the routine. It gets folded into the background noise of daily operations. Over time, what should be considered a red flag is dismissed as just the way that truck “feels.”
And trucks, like people, get old. The valves don’t respond as quickly. The air tanks don’t purge as often. The lines start to weep. But unless someone goes looking for these issues, they rarely rise to the top of the to-do list. After all, they don’t cause immediate downtime—until they do.
The truth is, the longer a fleet puts off serious attention to the air system, the greater the risk becomes. And this isn’t just about avoiding breakdowns—it’s about avoiding disaster. Because when an air system finally fails, it doesn’t usually do so gently. It does so in motion, under load, often in the worst possible conditions.
Winter’s Wake-Up Call
Cold weather has a way of exposing weak spots in any system, and air systems are no exception. Moisture that’s been quietly sitting in the lines through autumn can freeze solid overnight, blocking air flow and triggering brake failures without warning. A valve that seemed sluggish in September becomes completely unresponsive by December. A purge valve that failed silently in summer becomes a ticking time bomb come January.
And it’s not just about freezing. Cold air is dry, but the transition from warm to cold—especially in places where trucks run cross-country—creates the perfect storm for condensation. If dryers are failing, or tanks aren’t being properly drained, that water has nowhere to go. And once it’s in the lines, it's only a matter of time before it causes corrosion, clogs, or outright blockages.
This is when you see trailers that won’t release, tractors that can’t build pressure, and drivers stuck on the side of the road with a machine that, moments earlier, seemed perfectly fine.
It’s also when you see accidents.
The Human Factor
No piece of equipment exists in a vacuum. The health of a truck’s air system is ultimately tied to the habits and knowledge of the people maintaining and operating it. And in this area, the industry still has work to do.
Many younger drivers coming up today have never operated a rig without anti-lock brakes. Some have never been trained to recognize the slow onset of valve failure, or the subtle differences in brake response that signal moisture buildup. Technicians—especially in fast-paced shops—are often under pressure to get trucks in and out quickly, which means checks that aren’t legally required often get skipped.
Even experienced drivers can develop blind spots. Familiarity breeds complacency. When you’ve driven the same truck for years, it’s easy to overlook small changes in the way it feels. It’s easy to trust that the system will keep working because it always has.
But trust is not a maintenance strategy. And neither is hope.
Building a Better Baseline
Addressing air system failures doesn’t require reinventing the wheel. It just requires putting deliberate attention on what’s usually invisible. That means encouraging thorough pre- and post-trip inspections that include listening for leaks and feeling for delayed response. It means making air system servicing part of routine preventive maintenance, not just a winter prep item or an annual inspection box to check.
It also means making space—for training, for inspection, and for repair. Drivers need time to do real walkarounds. Shops need room in their schedules to do more than just fix what’s broken. And fleets need to build cultures that value the long view over short-term savings.
Because when an air system fails, you don’t just lose air pressure. You lose control. And in trucking, control is everything.
A Final Word
If there’s one thing I’ve learned after decades in this business, it’s that the quietest problems are often the most dangerous. And the air system is a perfect example. It doesn’t ask for attention. It doesn’t demand respect. But it deserves both.
So the next time you hear a slight hiss when you park the trailer, or you feel the brakes lag just a second longer than they used to, don’t brush it off. Don’t let it slide.
Because the air system may not cry out when it’s in trouble. But when it fails, it does so loudly—and often too late.