Mobile vs Fixed Truck Service: When Each Makes Sense
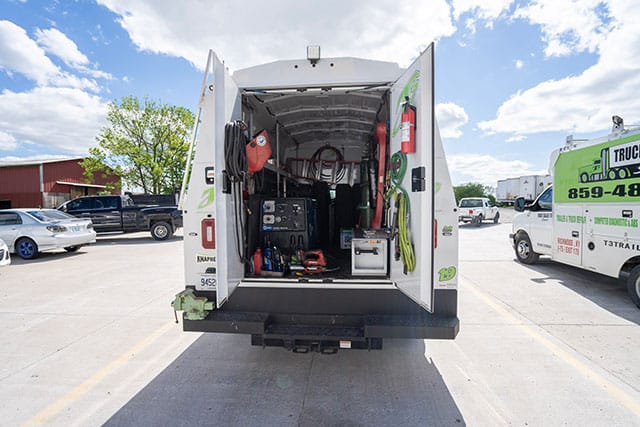
In the commercial trucking world, the debate between mobile and fixed service isn’t a matter of which is better. It’s a matter of which is right, and when.
For the men and women running fleets—whether you’ve got ten trucks or ten hundred—the decision to rely on mobile service vendors, traditional fixed-location shops, or some combination of both isn’t just logistical. It’s financial, operational, and at times deeply personal. It’s a decision that touches uptime, driver satisfaction, regulatory compliance, and ultimately the very rhythm of your business.
Let’s get this out of the way first: both mobile and fixed service solutions exist because both are necessary. The landscape of long-haul trucking is too vast, too varied, and too vulnerable to single-answer thinking. What works at a distribution center outside Dallas doesn’t always fly on I-80 in Wyoming.
But understanding why each makes sense in its own right, and when to rely on one over the other, is where the real value lies.
Fixed Base Maintenance: Predictable, Centralized, Controlled
Let’s start with the traditional fixed-location shop. This could be your own in-house garage or a relationship you maintain with a trusted service center along your regular freight corridors. These facilities are built for consistency. They’re staffed by mechanics who work under a roof, with stable lighting, proper tooling, and access to parts.
What they bring to the table is predictability.
A well-run shop is like a well-run kitchen. Parts are stocked, work orders flow in a managed queue, and there’s little risk of someone making decisions based on pressure from a roadside situation. Repairs here are often more thorough, more documented, and more traceable. If your business has a dedicated yard or terminal and your operations allow for downtime planning, it makes sense to consolidate work at a centralized fixed facility.
There’s also a safety dimension that rarely gets discussed but should. Some repairs should only happen in a controlled environment. Anything involving frame damage, air systems, or multi-axle braking work can be dangerous if rushed or done on the shoulder of a highway. In these cases, fixed service isn’t just practical—it’s responsible.
Fixed service also makes it easier to implement preventive maintenance schedules. When drivers bring units back to base, or to a known service partner on a recurring route, you're able to tie maintenance into operations with minimal disruption. You can track component lifespan. You can enforce standards. You can keep warranties intact. That kind of structure appeals to safety officers, fleet managers, and accountants alike.
But fixed service has its limits.
Mobile Service: Urgency, Reach, and Real-World Flexibility
Now let’s talk about mobile repair.
There’s a kind of brutal honesty in trucking: breakdowns don’t care about your schedule. Tires don’t blow near your yard. Starters don’t fail in daylight during shift changes. The unexpected happens in the dark, in the rain, on the outskirts of nowhere.
This is where mobile service earns its keep.
Mobile mechanics don’t just fix trucks—they preserve freight schedules, driver morale, and customer relationships. They’re often your first line of defense against full-blown chaos. And for smaller fleets without the budget or real estate for in-house service, mobile vendors are often the only practical option.
The real advantage of mobile service isn’t just that it brings the repair to the truck—it’s that it does so with minimal disruption to the bigger picture. A mobile tech might get your driver rolling again in two hours, where a tow and shop repair would’ve cost you twelve. They buy you time, which is the one resource you can’t stock on a shelf.
But mobile repairs, by nature, are constrained. You’re working outdoors, often in less-than-ideal conditions. You’re limited by the tools and parts you can carry. And some issues—particularly those involving engine diagnostics, structural work, or emissions systems—can go beyond what a mobile unit can or should do safely.
Still, for batteries, belts, brakes, lights, hoses, tire service, alternators, air leaks—you name it—mobile technicians are a lifeline. And in some regions, especially those with remote dispatch points or long-haul corridors, they’re not a backup plan—they’re the only plan.
It’s Not Either/Or—It’s Strategic Balance
The best fleets aren’t choosing between mobile and fixed. They’re blending both.
They think in terms of risk exposure. Where are the trucks? How often do they run through the same lanes? Where are the bottlenecks? What’s the cost of delay at different points in the journey?
They also factor in driver impact. Sitting on the side of the road for eight hours waiting for a tow isn’t just inefficient—it’s demoralizing. Drivers are human, and their experience matters. The perception of being supported—having someone show up with tools and answers—can be the difference between turnover and retention.
And then there’s the financial modeling. Fixed shops require investment—real estate, staffing, insurance, compliance. Mobile vendors offer flexibility and pay-per-use pricing, but with limits in scalability. Larger fleets might mix in-house facilities with mobile vendor contracts to create a hybrid coverage model. Smaller fleets may rely entirely on mobile repair but schedule annual fixed-site overhauls.
What matters is matching the solution to the situation.
If your fleet turns around at the same depot every two days, then fixed maintenance should be a cornerstone. If you’ve got trucks crossing five states in a week, your playbook better include mobile resources. And if you’re somewhere in between—running regional freight, balancing dedicated routes with spot market hauls—then your strategy probably lives in that hybrid middle ground.
What the Best Fleets Do
The most efficient fleets I’ve worked with don’t just react to breakdowns—they model for them. They map where trucks fail, why they fail, and what each minute of delay costs them. They don’t treat mobile repair as a last resort. They treat it as a component of operational agility.
They also communicate with drivers. They ensure that drivers know who to call, what to expect, and how to respond. And they train their dispatchers not just to assign routes, but to manage repair logistics with foresight.
It’s not about romanticizing mobile repair or glorifying in-house shops. It’s about choosing tools that make your business more resilient.
Because in trucking, it’s not about whether something will go wrong. It’s about what you’ve put in place to recover when it does.
Whether you’re the owner-operator of a single sleeper cab or the director of maintenance for a 300-unit fleet, your job isn’t to pick a side in the mobile vs fixed debate.
Your job is to understand where each fits, what each costs, and how each helps you protect the thing that matters most in this business: the road ahead.